How Can Transformer and Inverter Welders Impact Your Projects?
May 2, 2024
10 min read
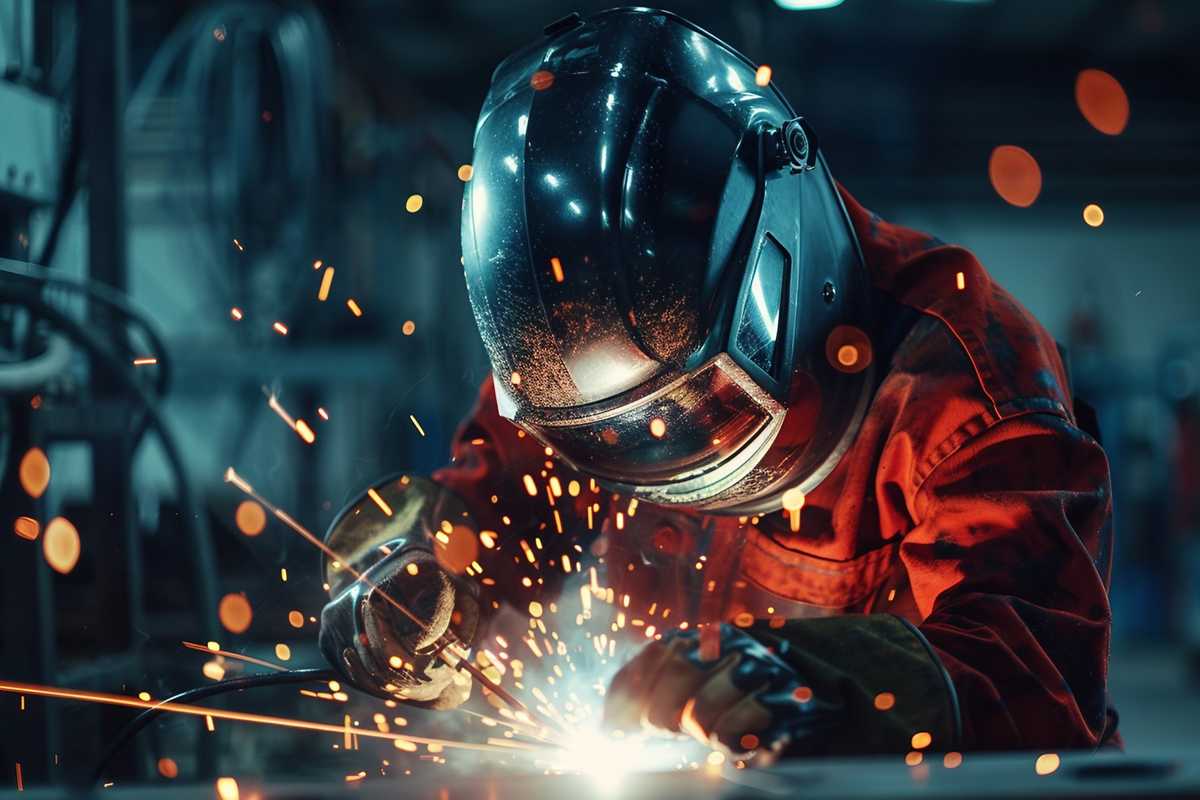
1. Introduction: The Evolution of Welding Technology
Welding has been a cornerstone of industrial progress, enabling us to join metals and materials in ways that have shaped our world. From the traditional hammering techniques of forge welding to the sophisticated processes of today, the journey of welding technology is a testament to human ingenuity. In this evolution, two significant milestones stand out: transformer and inverter welders. These tools have redefined efficiency and precision in the welding industry.
Transformer welders have been the go-to choice for decades, known for their durability and ease of use. They work by transforming electrical energy into the right voltage and current for welding, providing a steady and reliable source of power. Despite their widespread use, they have their drawbacks, including size, weight, and energy consumption.
In contrast, inverter welders are the modern marvels of the welding world. They take electrical power, increase its frequency, and then convert it back, allowing for a more compact design and better energy efficiency. This technology has quickly become favored for its versatility and the superior control it offers welders, making it suitable for a wide range of applications.
As we explore the intricacies of these two types of welders, we'll help you understand which might be the best fit for your projects. Whether you're a seasoned welder or just starting, the choice between a transformer and an inverter welder can greatly influence your work's outcome. Let's dive into the details of each technology, their benefits, and limitations, to guide you in making an informed decision for your welding needs.
2. Welding Technology: A Comparative Look at Transformer and Inverter Welders
Welding technology is essential in various industries, from construction to manufacturing. It involves fusing materials together, typically metals or thermoplastics, by melting them with a filler to create a strong bond. As technology has advanced, so have the tools we use for welding, leading to the development of transformer and inverter welders, each with distinct characteristics suited to different tasks.
Transformer Welders: The Traditional Workhorses
Transformer welders have been the standard in the industry for years. They are known for their straightforward design and dependability. These machines step down the voltage from the power supply to create a stable welding current. Because of their simple construction, they are durable and generally more affordable than inverter welders. They're also easier to maintain due to their fewer electronic parts.
However, transformer welders are not without their drawbacks. They are typically heavier and larger, making them less ideal for jobs that require moving the equipment around. They also consume more energy, which can lead to higher electricity costs over time. Additionally, they offer less control over the welding arc, which can be a limitation for more intricate welding jobs.
Inverter Welders: The Modern Innovators
Inverter welders are the newer generation of welding technology. They use advanced electronics to convert and control the power supply at a higher frequency, which allows for a more compact and lightweight design. This makes them perfect for jobs that demand mobility.
The advantages of inverter welders are clear:
- They are more energy-efficient, which can lead to cost savings on electricity in the long run.
- They provide better control over the welding arc, with adjustable settings that can enhance the quality of the welds.
However, inverter welders come with their own set of challenges:
- They are generally more expensive initially, which can be a barrier for some buyers.
- The complexity of their electronics means they can be more prone to issues if not properly cared for.
- They require a stable power supply, as they are sensitive to fluctuations in power.
In conclusion, both transformer and inverter welders have their place in the welding world. Transformer welders are reliable and cost-effective, making them suitable for heavy-duty tasks where portability isn't a concern. Inverter welders, on the other hand, offer advanced features and portability, ideal for a variety of welding situations, especially where precision and energy efficiency are valued. Your choice between the two should be guided by the specific needs of your welding projects, considering factors such as budget, work environment, and the necessity for portability.
3. In-Depth Performance Analysis: Inverter vs. Transformer Welders
Choosing the ideal welder hinges on understanding their performance in real-world scenarios. Inverter and transformer welders each bring their strengths to the table, impacting their suitability for different welding tasks. We'll break down the critical aspects of arc stability, energy efficiency, and long-term reliability to guide your selection process.
Fine-Tuning the Arc: Stability and Precision
A stable arc is the cornerstone of a quality weld. Transformer welders are known for their consistent output, which simplifies the welding process, making them a solid choice for those new to welding or when exact precision isn't paramount.
In contrast, inverter welders shine in arc control, offering a level of precision that caters to skilled tasks. Their advanced electronics allow for rapid adjustments to the arc, facilitating a smoother weld on delicate materials or intricate jobs. This precision is particularly advantageous for specialized welding techniques like TIG welding, where the quality of the arc is paramount.
Cutting Costs with Efficiency: Energy Use Matters
Energy efficiency isn't just about saving the planet—it's also about saving money. Inverter welders excel in this area by using high-frequency AC power, which requires a smaller transformer and leads to less energy waste. This efficiency translates to lower electricity bills, a benefit that becomes more pronounced with frequent use.
On the flip side, transformer welders are less energy-efficient, drawing more power and potentially increasing operational costs. However, for those who weld occasionally or prioritize upfront savings, the higher energy use of transformer welders may not be a significant concern.
Built to Last: Weighing Durability Against Innovation
The longevity of your welder is vital, especially for professionals who depend on their tools. Transformer welders have earned their reputation for durability, with a simpler design that's less prone to malfunctions and can endure tough conditions. They are the go-to for industrial settings where the welder is in constant use and must withstand rigorous demands.
Inverter welders, while packed with modern technology, have made strides in reliability. They are designed to endure and maintain performance levels, but they do house sensitive electronics that might need more attentive care. In environments with prevalent dust, moisture, or other contaminants, the resilience of an inverter welder could be tested.
In summing up, inverter welders are the frontrunners in arc control and energy savings, whereas transformer welders take the lead in ruggedness and straightforward operation. Your decision should align with your welding projects' specific needs, considering the precision required, usage frequency, and the work setting.
4. Making the Smart Choice: Practical Aspects of Welder Selection
Choosing the right welder goes beyond just comparing technical specs; it's about understanding how your choice will fit into your daily work and affect your wallet over time. Let's break down the key practical factors that should influence your decision.
Upfront Costs vs. Long-Term Savings
The price tag you see in the store isn't the end of the story. Yes, transformer welders usually cost less at the outset, but don't forget to think about the future. Inverter welders might have a higher price initially, but they're like energy-saving light bulbs—they could reduce your electricity bills because they're designed to use power more efficiently. Also, consider repair costs. Transformer welders are often less expensive to fix since they have a less complex design.
The Right Welder for Your Workspace
Think about where you'll be using your welder. If you're in a workshop or factory and your welder will stay put, the sturdy build of a transformer welder could be perfect. They're built tough and can handle the grind of heavy-duty work. But if you're always on the move or working in different places, an inverter welder's lighter weight and compact size will be your best friend. They're adaptable, too, ready to tackle various metals and welding positions, whether you're indoors or out in the field.
Portability and User-Friendly Features
If you're a roving welder, carrying a heavy machine from job to job isn't going to be fun. Inverter welders score big here—they're lighter and easier to transport, ideal for those who need to be mobile, like on construction sites or for repairs out and about.
Ease of use is also key. Inverter welders often come with digital displays and straightforward controls that help you get precise results without a fuss. This is especially helpful if you're still getting the hang of welding or dealing with complex projects.
When you're weighing your options, match these practical points to your specific situation. If keeping costs down is your main concern and you're in a fixed spot, a transformer welder could be the way to go. But if you need the freedom to move around, care about saving energy, and want a machine that's easy to handle, investing in an inverter welder might be the smarter move for the long haul. Choose with an eye on the future to ensure your welder meets your needs today and for many projects to come.
5. Final Thoughts: Choosing the Ideal Welder for Your Needs
In the quest to find the perfect welder for your projects, the choice between inverter and transformer models is pivotal. Each has its own set of advantages tailored to meet different welding requirements.
Transformer welders are the stalwarts of the welding world, prized for their durability and consistent performance. They're particularly well-suited for intensive welding tasks in stable environments where their size and weight aren't issues. Their energy consumption is higher, which might be a concern for some, but their proven track record in industrial settings is undeniable.
Inverter welders, on the other hand, are the embodiment of modern welding innovation. They stand out for their energy efficiency and the precise control they offer over the welding process. Their compact and lightweight design makes them a top pick for welders who need to move around frequently or work in tight spaces. While the upfront cost is higher, the potential for energy savings and the versatility they provide often make up for the initial investment.
Your decision should hinge on the specific demands of your welding projects. If you're dealing with large-scale, repetitive work that doesn't require moving the equipment, a transformer welder could be your best bet. If your work involves a variety of welding jobs, particularly in locations without easy access to power or where detailed work is necessary, an inverter welder is likely the superior choice.
In making your selection, balance the initial cost against the expected performance and practical benefits. Consider the long-term implications of your choice, such as potential energy savings, ease of transport, and adaptability to different welding scenarios. By carefully evaluating the strengths and limitations of each welder type, you can make a well-informed decision that will lead to efficient, high-quality welding results. Whether you lean towards the tried-and-true transformer welders or opt for the cutting-edge inverter models, the right equipment will be a valuable ally in your welding pursuits.
Sharing is Caring
Feedback
At WeldWins, we know we aren't perfect which is why we're always looking for ways to improve. You can help us do better by taking 2 minutes to fill out our simple feedback form.
Any and all feedback is welcome. It could be a complaint, an idea, or even just a comment, we'll always be grateful to hear what you think.