How Can You Master Different Weld Joints for Stronger Structures?
June 30, 2024
9 min read
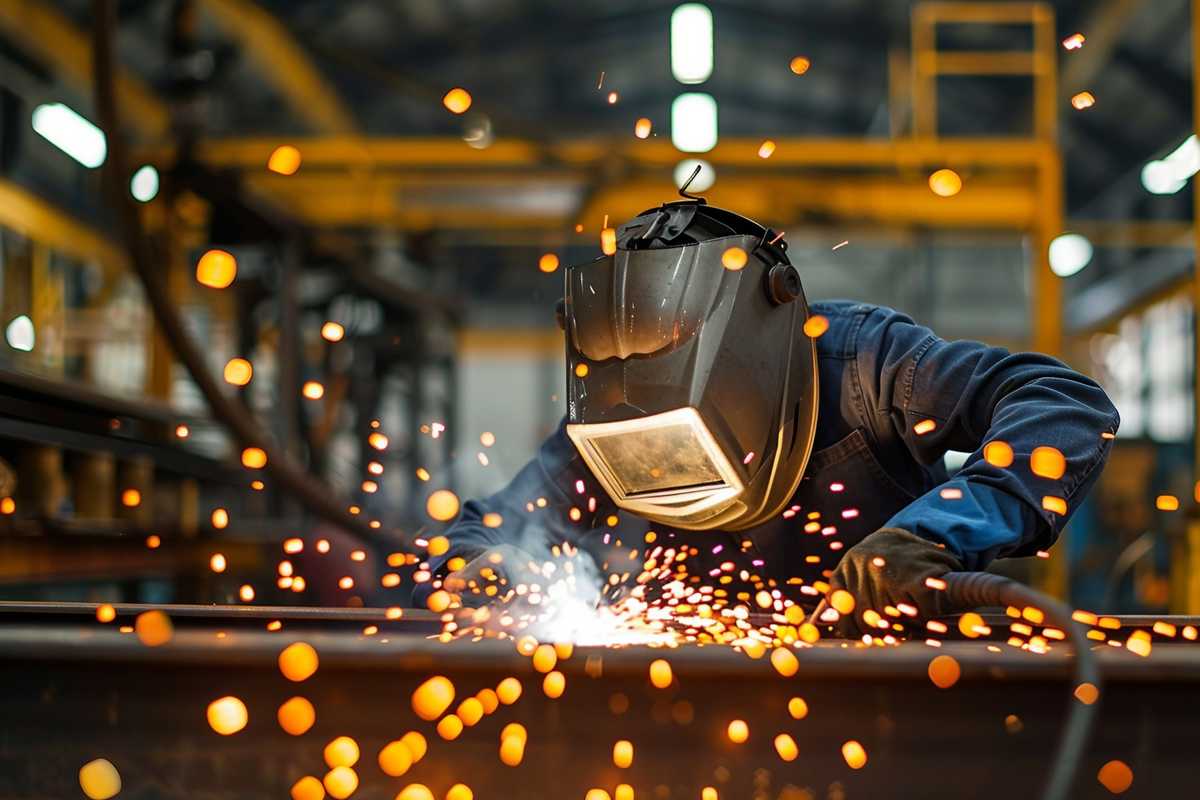
Welcome to the essential guide to weld joints, where we fuse practical know-how with expert insights to elevate your welding craft. Welding isn't just about joining metals; it's about creating enduring bonds that withstand the tests of time and stress. Whether you're a skilled artisan or just starting out, grasping the nuances of different weld joints is crucial for any project's success.
In this guide, we'll dissect the anatomy of weld joints, from the common butt joint to the intricate lap and edge joints. We'll arm you with the knowledge to pick the perfect joint for your task and the finesse to execute it flawlessly.
But we won't stop at the "what"—we'll dive deep into the "how." Through expert-backed advice, step-by-step tips, and vivid examples, we're here to refine your welding techniques. Whether piecing together a basic structure or tackling a complex design, the skills you'll gain are set to make your welds robust and dependable.
So, let's light up our torches and embark on this journey to welding excellence. By the end of this guide, you'll be well-equipped to ensure that your welding projects are not only successful but also safe and enduring.
1. Exploring the Five Main Weld Joints
In the world of welding, the strength and stability of a structure hinge on choosing the right type of weld joint. Each joint type is tailored to specific structural needs and applications. We'll take a closer look at the five primary weld joints, highlighting their distinct features and when to use them.
The Basic Butt Joint
Imagine two metal plates lying flat, end-to-end—this is where a butt joint comes into play. It's straightforward and widely used, especially when you need a smooth, continuous surface. Picture the seamless construction of a pipeline or the sturdy framework of a building; that's the butt joint's handiwork. For a top-notch butt joint, aligning the pieces precisely is key to a strong, flawless connection.
The Sturdy Tee Joint
When two pieces of metal meet at a 90-degree angle, forming a 'T', you've got a tee joint. It's a mainstay in frames and structures that require a branch connection. Imagine the skeleton of a bicycle or the legs of a table, relying on the tee joint's robustness to handle weight and stress. Achieving deep penetration into the base metals is crucial for a tee joint that's up to the task.
The Aesthetic Corner Joint
Corner joints come into play when you're crafting something like a picture frame or a box, where two metal parts join at a corner. It's not just about strength here; the appearance matters too. To avoid any unsightly defects, such as cracks, it's essential to prepare the joint well and apply the right welding technique.
The Overlapping Lap Joint
When one metal piece overlaps another, we use a lap joint. This joint is particularly useful when connecting pieces of different thicknesses or for simplicity in assembly. Think of a set of stairs with overlapping steps. However, lap joints can be tricky—they're susceptible to tearing if not handled carefully. The right welding approach can prevent such issues, ensuring a durable lap joint.
The Precise Edge Joint
Edge joints are a bit rarer, but they shine in sheet metal work. When the edges of two thin metal sheets lie side by side, an edge joint neatly binds them together. It's less about bearing loads and more about precision and a clean finish. A steady hand and careful welding can produce an edge joint that's both strong and visually pleasing.
By mastering these five weld joints, you'll be equipped to tackle a variety of projects with confidence. Each joint has its place, and knowing which to use and how to execute it can make all the difference in the durability and integrity of your work.
2. Fine-Tuning Your Welding Approach for Different Joint Types
To excel in welding, it's not enough to know the various joint types; you must also master the specific techniques that make each weld strong and aesthetically pleasing. In this section, we'll guide you through the tailored approaches for each joint type, ensuring your welding projects are not only structurally sound but also visually impressive.
Perfecting the Butt Joint
Butt joints are the go-to when you need a seamless and strong connection, like in pipeline construction. The secret to a perfect butt joint lies in preparing the metal edges meticulously. Beveling the edges allows for deeper weld penetration, which translates to a more robust joint. Consistent welding speed and temperature are your best friends here, helping you avoid common pitfalls such as undercutting or overbuilding the weld.
Mastering the Tee Joint
Tee joints are the backbone of structures that require a perpendicular connection, like the cross-section of a metal fence. Achieving a solid tee joint starts with excellent penetration at the joint's root. A weaving motion with the electrode can evenly spread the heat, reducing the risk of weak spots. Selecting the right electrode size and type is also critical to prevent issues such as porosity, which can compromise the joint's integrity.
Crafting Quality Corner Joints
Corner joints are all about precision, especially in frames or boxes where aesthetics are as important as strength. Start with a clean metal surface to avoid any weld contamination. Keep an eye on the weld puddle and aim for a consistent bead size for a neat finish. For load-bearing corners, a backer plate can offer extra support, ensuring the joint is up to the task.
Ensuring Strong Lap Joints
Lap joints are simple yet powerful, often used in steps or layered metal designs. To prevent lamellar tearing, a common defect in lap joints, it's essential to control the welding sequence to reduce stress buildup. Opt for a low-hydrogen electrode to minimize the risk of cracking and adjust the heat input carefully to prevent warping or burning through, especially with thinner materials.
Achieving Precise Edge Joints
Edge joints may be less frequent, but they're crucial in sheet metal work where edges come together. The key to a successful edge joint is a steady hand and a series of short, overlapping welds that control distortion and heat input. Tacking the pieces in place before the final weld can ensure proper alignment and stability.
By adopting these specialized techniques for each joint type, you'll not only improve the quality of your work but also ensure the longevity and safety of your welds. Remember, the devil is in the details, and with practice and precision, your welding projects will stand out for their excellence.
3. Ensuring a Safe Welding Environment
Welding is a powerful craft that requires a deep respect for safety and meticulous preparation. To embark on any welding project, it's essential to establish a secure environment that protects you and others from potential hazards. Here's a step-by-step guide to setting up a safe welding space.
Gear Up with the Right Protection
Your first line of defense in welding is proper Personal Protective Equipment (PPE). Suit up with a welding helmet featuring an auto-darkening lens to guard against intense light and harmful UV rays. Wear fire-resistant gloves to protect your hands from heat and sparks, and dress in flame-resistant garments to cover exposed skin. Always have safety glasses on under your helmet for an extra layer of eye safety.
Breathe Easy with Proper Ventilation
Welding fumes are not something to take lightly. Make sure your workspace is airy, with fresh air circulating to disperse toxic gases. If you're in a confined space, set up a fume extraction system or position portable fans to direct fumes away from your breathing zone.
Organize Your Workspace
A clutter-free area is a safer area. Clear out any unnecessary items, especially flammable materials, to minimize fire risks. Keep walkways free of obstructions to avoid trips and falls. Always have a fire extinguisher within arm's reach, and ensure the floor is dry to prevent slips and electric shocks.
Check Your Tools and Equipment
A thorough equipment check is non-negotiable. Examine your welding tools for any signs of damage, such as frayed cables or loose connections. Make sure your welding machine is in top working order. Regular checks and maintenance can head off mishaps and keep your welding process smooth.
Know Your Metals
Different metals behave differently under the welder's torch. Get to know the metals you're working with—their melting points, how they conduct heat, and how they react to being welded. This knowledge is crucial for choosing the right welding settings and techniques.
Master Your Welding Technique
Before you dive into the main event, review the welding method you'll be using. Whether it's MIG, TIG, or Stick welding, each technique has its own safety protocols and best practices. Practice beforehand to ensure you're comfortable and confident with the process.
By following these safety protocols and preparation steps, you'll not only safeguard your well-being but also set the stage for high-quality welding results. Safety isn't just a precaution; it's the bedrock of professional welding.
4. Solidifying Your Welding Mastery: A Final Word
In closing, we've journeyed through the essential landscape of weld joints, uncovering the pivotal role they play in the art of welding. We've dissected each joint type, from the ubiquitous butt joint to the specialized edge joint, and provided you with the insights to select and execute them with precision.
Throughout this guide, we've emphasized the importance of technique and attention to detail. For instance, when tackling a butt joint, remember the importance of beveling the edges for deep penetration and strength. Or consider the corner joint, where a clean surface and consistent bead size are vital for both structural integrity and visual appeal.
We've also underscored the critical nature of safety and preparation. It's a simple truth that no welding project is worth compromising your well-being. By donning the right protective gear, maintaining a well-ventilated workspace, and conducting regular equipment checks, you create a foundation for both safety and success.
This guide has aimed to arm you with practical knowledge and actionable strategies. By applying these principles, you'll elevate your welding projects from mere metal connections to enduring constructions that resist wear and tear.
As you continue to hone your skills, stay abreast of the latest advancements in welding technology and techniques. Your commitment to learning and safety will ensure that your welds are not just strong, but exemplary.
Forge ahead with confidence, knowing that with each spark and bead, you're not just joining metals—you're crafting the backbone of structures that last.
Sharing is Caring
Feedback
At WeldWins, we know we aren't perfect which is why we're always looking for ways to improve. You can help us do better by taking 2 minutes to fill out our simple feedback form.
Any and all feedback is welcome. It could be a complaint, an idea, or even just a comment, we'll always be grateful to hear what you think.