What Are the Key Differences Between MIG and MAG Welding?
May 30, 2024
11 min read
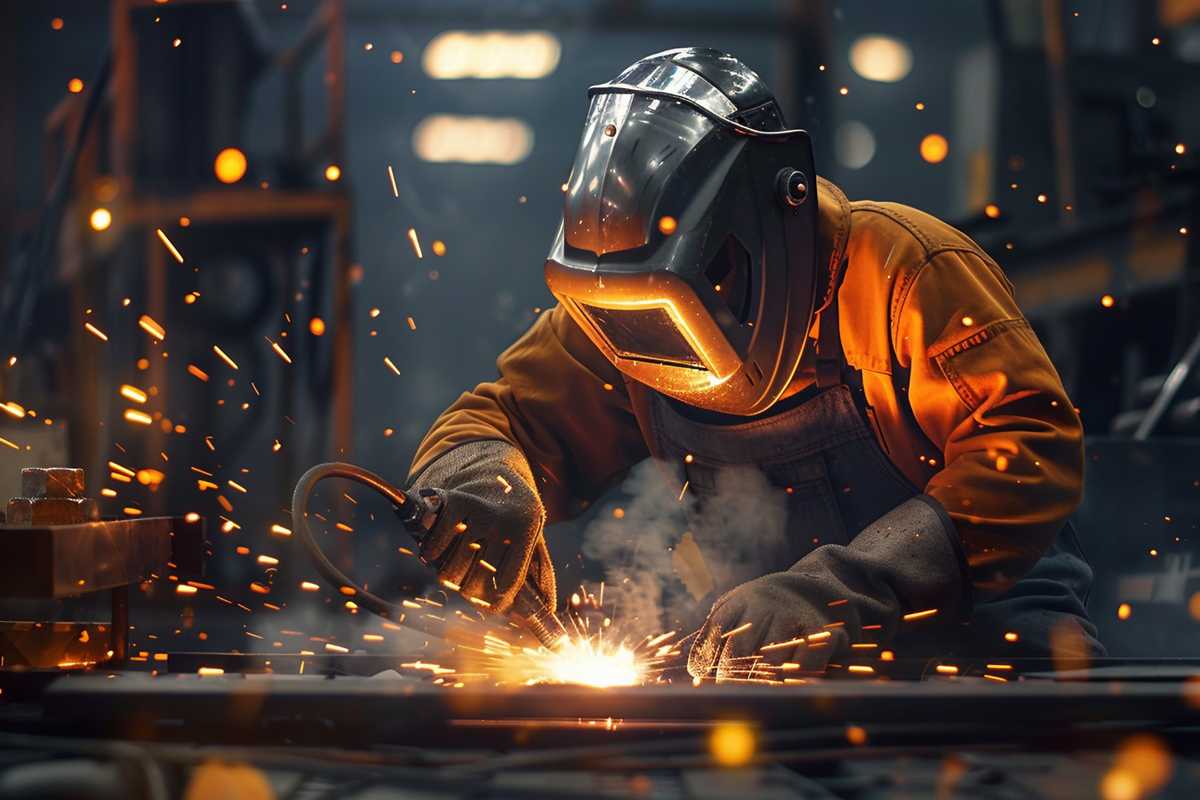
Welding is not just a skill; it's an intricate dance of science and craftsmanship that brings to life the structures we rely on every day. Among the myriad of welding techniques, Gas Metal Arc Welding (GMAW) shines as a favorite for its adaptability and the superior strength of its welds. This method is beloved by both seasoned professionals and enthusiastic hobbyists for its straightforward application and reliable results.
Yet, within the GMAW family, there's a common mix-up between its two main branches: Metal Inert Gas (MIG) welding and Metal Active Gas (MAG) welding. These twins in the welding world may look alike at first glance, but they have distinct differences, primarily in the shielding gases they use. This seemingly small variation can have a big impact on the welding process and the final product.
In this comprehensive guide, we'll delve into the heart of GMAW, clarifying the key distinctions between MIG and MAG welding. Whether you're just starting out in welding or looking to refine your skills, a clear understanding of these techniques is vital for crafting strong, resilient welds. Join us as we navigate through the specifics of these welding methods, equipping you with the knowledge to excel in your welding projects.
1. Demystifying GMAW: The Essentials of Gas Metal Arc Welding
Gas Metal Arc Welding (GMAW) stands as a cornerstone in the world of metal fabrication, offering a fusion of speed, efficiency, and strength. This welding technique harnesses the power of an electric arc to melt and merge metals, utilizing a consumable wire electrode that doubles as a filler material. As the electrode feeds through the welding gun, it not only bridges the gap between workpieces but also carries the current that sustains the arc.
The success of GMAW hinges on the protective bubble created by shielding gas, which is vital in safeguarding the molten weld pool from the detrimental effects of atmospheric gases like oxygen and nitrogen. Without this shield, the weld could succumb to porosity, a defect where trapped gas weakens the joint.
The choice of shielding gas is not a one-size-fits-all; it varies depending on the specific GMAW method in use. Broadly, gases fall into two categories: inert, which remain passive during the welding process, and active, which can chemically interact with the molten metal. This distinction gives rise to the two primary GMAW subtypes: Metal Inert Gas (MIG) welding and Metal Active Gas (MAG) welding.
To truly grasp GMAW, one must appreciate the synergy between the electric arc, the wire electrode, and the shielding gas. This trio works in concert to make GMAW a versatile and preferred method for creating durable welds in a myriad of applications, from industrial fabrication to home-based DIY projects.
2. MIG Welding: Harnessing Inert Gases for Pristine Welds
MIG welding, a key technique within the Gas Metal Arc Welding (GMAW) family, is renowned for its ability to cleanly and efficiently join metals. This process is characterized by the use of inert gases, such as argon or helium, which act as a shield to protect the molten metal from the negative effects of the air around us.
The versatility of MIG welding is one of its standout features. It's capable of fusing a diverse array of metals and alloys, from the lightweight aluminum used in bike frames to the sturdy stainless steel found in kitchen sinks, and it can handle materials of varying thicknesses with ease. This adaptability makes it a favored choice in sectors that demand robust and reliable welds, such as the automotive industry, where it's used to assemble cars, and in construction, where it helps erect buildings.
Ease of use is another hallmark of MIG welding. The process involves a continuous wire feed, which serves a dual purpose as both the electrode and the filler material, streamlining the welding operation. The inert gases facilitate the production of smooth, slag-free welds, which means there's little to no cleanup required afterward. This is especially beneficial when the appearance of the weld is important, or when working with metals that are prone to rust or tarnish.
Despite its many benefits, MIG welding does come with some drawbacks. The cost of the equipment and the inert gases can be higher than other welding methods. Additionally, MIG welding can be less effective in windy conditions or outdoor environments since the wind can blow away the protective gas shield, potentially compromising the weld's integrity. To counter this, welders might need to set up wind barriers or opt to weld indoors, which isn't always feasible.
In essence, MIG welding offers a pristine and efficient method for joining metals, with its advantages of versatility, user-friendliness, and high-quality outcomes making it a popular choice for a wide range of welding tasks. However, it's important to consider the costs and the potential impact of environmental factors when opting for this method.
3. Exploring MAG Welding: The Role of Active Gases
MAG welding, short for Metal Active Gas welding, is a specialized branch of the Gas Metal Arc Welding (GMAW) family. This method stands out because it uses active gases, such as carbon dioxide (CO2) and sometimes oxygen (O2), often combined with inert gases like argon. These active gases are not just bystanders; they actively engage with the molten metal, affecting the arc's stability, the transfer of metal, and ultimately the strength and quality of the weld.
The interaction between the active gases and the molten metal can result in a more consistent arc and deeper penetration, making MAG welding particularly effective for joining thicker materials. It's a common choice in industries that work with ferrous metals—those containing iron—like carbon steel and stainless steel. You'll find MAG welding in action on construction sites for buildings and bridges, as well as in factories producing vehicles and heavy equipment.
One of the main benefits of MAG welding is its efficiency. It boasts a high deposition rate, meaning it can lay down a lot of weld metal quickly, which is a huge plus for large projects or when time is tight. It's also adaptable; by tweaking the gas mix and welding settings, you can tailor the process to different materials and thicknesses.
However, MAG welding isn't without its challenges. The active gases can cause more spatter—those pesky droplets of molten metal that scatter during welding—leading to extra cleanup time. They can also increase the risk of oxidation in the weld, which might necessitate further treatments to maintain the weld's integrity.
In essence, MAG welding is a robust and efficient choice within the GMAW techniques, ideal for projects involving iron-rich metals. Its distinctive use of active gases offers both benefits and challenges, and understanding these is crucial for any welder aiming to perfect their craft in GMAW and choose the best method for their project's needs.
4. Deciphering the Differences: MIG vs. MAG Welding
In the realm of Gas Metal Arc Welding (GMAW), the choice between Metal Inert Gas (MIG) and Metal Active Gas (MAG) welding can significantly impact the outcome of your project. Both techniques may seem similar, utilizing a wire electrode and shielding gas, but the gas type is a game-changer, influencing everything from the weld's appearance to its strength.
Breaking Down the Distinctions
Shielding Gas: The Decisive Factor
- MIG welding employs inert gases like argon or helium, which remain neutral during the welding process. This results in a clean and uncontaminated weld, preserving the metal's natural properties.
- MAG welding, however, uses active gases such as a carbon dioxide and argon mixture. These gases engage with the metal, potentially altering the weld's behavior and finish.
Arc Behavior and Weld Quality
- MIG's inert gases lead to a steady arc and less spatter, simplifying the creation of a neat, aesthetically pleasing weld.
- With MAG, the active gases can cause more spatter and a somewhat erratic arc. However, they contribute to deeper weld penetration, which is crucial for joining thicker materials.
Choosing Based on Metal
- MIG shines when welding non-ferrous metals, including aluminum and stainless steel, due to its non-reactive nature.
- MAG is the go-to for ferrous metals like carbon steel, where its active gases can handle the material's characteristics effectively.
Cost Efficiency
- The specialty inert gases for MIG come with a higher price tag, which might add up for extensive projects.
- MAG welding is often more budget-friendly, especially when dealing with larger volumes or thicker sections.
Quick Comparison Guide
Aspect | MIG Welding | MAG Welding |
---|---|---|
Gas Type | Inert (e.g., Argon) | Active (e.g., CO2 mix) |
Metal Reaction | Non-reactive | Reactive |
Arc Stability | High | Variable |
Spatter Level | Low | Higher |
Weld Penetration | Moderate | Deep |
Best for Metals | Non-ferrous | Ferrous |
Cost | More expensive | More economical |
Armed with this knowledge, you can make a well-informed choice between MIG and MAG welding. If your project demands precision and a clean finish, MIG is your ally. For industrial-strength welds on thicker materials, MAG is your robust companion.
It's worth noting that many welders are adept at both MIG and MAG welding, switching between them based on the project's demands. By becoming proficient in both, you'll be prepared to tackle a diverse array of welding challenges with confidence and skill.
5. Making the Right Choice: MIG vs. MAG Welding
Selecting the appropriate welding process is crucial for the success of your project. It's not just about understanding the technicalities of MIG and MAG welding; it's about considering how these methods align with the specific demands of your work. Let's break down the key factors that will guide you in choosing the most suitable welding technique for your needs.
Assessing the Metals
The nature of the metal you're joining is a primary factor in your decision. MIG welding excels with non-ferrous metals like aluminum and copper, where its inert gases, such as argon, create a clean environment that prevents oxidation. In contrast, MAG welding is the preferred choice for ferrous metals, including carbon steel and stainless steel. The active gases used in MAG welding, like carbon dioxide, play a role in controlling the weld pool and ensuring a strong bond despite the heat.
Project Specifics
Your project's details can dictate the best welding method. If you're aiming for a high-quality finish with little post-weld cleaning, MIG welding is your best bet. However, if you're working outdoors or in breezy conditions where the wind could blow away the shielding gas, MAG welding's active gases are less vulnerable to dispersion, making it a more practical option.
Position and Precision
The welding position matters. For flat or horizontal welds, MIG welding is often the go-to due to its superior control over the weld pool. If you're dealing with vertical or overhead welding, MAG welding might be more forgiving, as its active gases aid in stabilizing the weld pool in these challenging positions.
Cost Considerations
Budget constraints can influence your choice. The inert gases for MIG welding, such as argon or helium, tend to be pricier than the active gases used in MAG welding. Moreover, the availability of these gases in your region could sway your decision.
Welder's Expertise
Finally, take into account the welder's experience. MIG welding is generally easier to pick up, making it a solid option for novices. MAG welding requires a more experienced hand to manage the active gases and the weld pool dynamics.
By carefully evaluating these factors—material type, project requirements, welding position, cost, and skill level—you can confidently choose between MIG and MAG welding. Each method offers unique benefits, and the optimal choice will depend on the specific needs of your project. Always balance the strengths and limitations of each process against the demands of your work to achieve the best results.
6. Final Thoughts: Mastering the Craft of GMAW
As we conclude our journey through the intricacies of Gas Metal Arc Welding (GMAW), it's clear that both MIG and MAG welding have their unique roles in the fabrication landscape. The choice of shielding gas—whether inert for MIG or active for MAG—determines the suitability of each method for different materials and projects.
MIG welding is the go-to for precision work on non-ferrous metals like aluminum, where its inert gas shield ensures a smooth, clean finish with minimal cleanup. It's perfect for tasks where aesthetics are as important as strength, such as in custom automotive work or art installations.
Conversely, MAG welding's active gases make it a powerhouse for robust, industrial applications involving ferrous metals like steel. It's a cost-effective solution for large-scale constructions or manufacturing processes where speed and penetration depth are critical.
Your project's success hinges on selecting the right welding technique. Consider the metal type, the desired weld appearance, environmental conditions, and your budget. With practice and a thorough understanding of GMAW's principles, you'll develop the proficiency to choose confidently between MIG and MAG welding, ensuring high-quality results every time.
Embrace the learning curve and experiment with both methods to expand your welding capabilities. As you do, you'll become more versatile and capable of tackling a broader range of projects with skill and assurance.
Sharing is Caring
Feedback
At WeldWins, we know we aren't perfect which is why we're always looking for ways to improve. You can help us do better by taking 2 minutes to fill out our simple feedback form.
Any and all feedback is welcome. It could be a complaint, an idea, or even just a comment, we'll always be grateful to hear what you think.